Vaneri on valmistettu kolmesta tai useammasta ohuesta puukerroksesta, jotka on liimattu yhteen liimalla. Jokainen puukerros eli vaneri on yleensä suunnattu siten, että sen syyt ovat suorassa kulmassa viereiseen kerrokseen nähden kutistumisen vähentämiseksi ja valmiin kappaleen lujuuden parantamiseksi. Useimmat vanerit puristetaan suuriksi, tasaisiksi levyiksi, joita käytetään rakentamisessa. Muut vanerikappaleet voidaan muotoilla yksinkertaisiksi tai yhdistelmäkäyriksi käytettäväksi huonekaluissa, veneissä ja lentokoneissa.
Ohuiden puukerrosten käyttö rakennusmateriaalina juontaa juurensa noin vuoteen 1500 eaa., kun egyptiläiset käsityöläiset liimasivat ohuita tumman eebenpuun paloja kuningas Tut-Ankh-Amonin haudasta löydetyn setripuisen arkun ulkopintaan. Kreikkalaiset ja roomalaiset käyttivät tätä tekniikkaa myöhemmin hienojen huonekalujen ja muiden koriste-esineiden valmistukseen. 1600-luvulla huonekalujen koristelu ohuilla puukappaleilla tuli tunnetuksi viilutuksena, ja itse puukappaleet tunnettiin viiluina.
1700-luvun lopulle asti viilupalat leikattiin kokonaan käsin. Vuonna 1797 englantilainen Sir Samuel Bentham haki patentteja useille viiluja valmistaville koneille. Patenttihakemuksissaan hän kuvaili useiden viilukerrosten laminointia liimalla paksumman kappaleen muodostamiseksi – ensimmäinen kuvaus siitä, mitä nykyään kutsumme vaneriksi.
Tästä kehityksestä huolimatta kesti lähes sata vuotta ennen kuin laminaattiviiluille löydettiin kaupallista käyttöä huonekaluteollisuuden ulkopuolella. Noin vuonna 1890 laminaattipuuta käytettiin ensimmäisen kerran ovien rakentamiseen. Kysynnän kasvaessa useat yritykset alkoivat tuottaa monikerroksisia laminaattilevyjä paitsi oviin, myös junavaunuihin, linja-autoihin ja lentokoneisiin. Tästä lisääntyneestä käytöstä huolimatta "liimapuun" käyttö, kuten jotkut käsityöläiset niitä sarkastisesti kutsuivat, loi tuotteelle negatiivisen kuvan. Tämän kuvan torjumiseksi laminaattipuun valmistajat tapasivat ja päätyivät lopulta käyttämään termiä "vaneri" kuvaamaan uutta materiaalia.
Vuonna 1928 Yhdysvalloissa esiteltiin ensimmäiset standardikokoiset 4 jalkaa x 8 jalkaa (1,2 m x 2,4 m) vanerilevyt yleiseksi rakennusmateriaaliksi. Seuraavien vuosikymmenten aikana parannetut liimat ja uudet tuotantomenetelmät mahdollistivat vanerin käytön monenlaisissa sovelluksissa. Nykyään vaneri on korvannut sahatun puutavaran monissa rakennustarkoituksissa, ja vanerin valmistuksesta on tullut miljardien dollarien maailmanlaajuinen teollisuudenala.
Vanerin ulkokerroksia kutsutaan vastaavasti etu- ja takakerroksiksi. Etupuoli on pinta, jota käytetään tai nähdään, kun taas takapuoli pysyy käyttämättömänä tai piilossa. Keskimmäinen kerros tunnetaan ytimenä. Viidestä tai useammasta langasta koostuvissa vanereissa välikerroksia kutsutaan ristikkäiskerroksiksi.
Vaneri voidaan valmistaa lehtipuista, havupuista tai näiden kahden yhdistelmästä. Joitakin yleisiä lehtipuita ovat saarni, vaahtera, mahonki, tammi ja tiikki. Yleisin vanerin valmistukseen käytetty havupuu Yhdysvalloissa on Douglas-kuusi, vaikka käytetään myös useita mänty-, setri-, kuusi- ja punapuulajikkeita.
Komposiittivanerissa on reunat reunaan liitettyjä lastulevy- tai massiivipuukappaleita. Se on viimeistelty vaneriviilulla sekä edessä että takana. Komposiittivaneria käytetään silloin, kun tarvitaan erittäin paksuja levyjä.
Puukerrosten yhteenliittämiseen käytettävän liiman tyyppi riippuu valmiin vanerin erityisestä käyttötarkoituksesta. Rakenteen ulkopuolelle asennettaviksi suunnitelluissa havupuuvanerilevyissä käytetään yleensä fenoliformaldehydihartsia liimana sen erinomaisen lujuuden ja kosteudenkestävyyden vuoksi. Rakenteen sisäpuolelle asennettaviksi suunnitelluissa havupuuvanerilevyissä voidaan käyttää veriproteiini- tai soijaproteiiniliimaa, vaikka useimmat havupuun sisälevyt valmistetaan nykyään samasta fenoliformaldehydihartsista kuin ulkolevyt. Sisäkäyttöön ja huonekalujen rakentamiseen käytetty lehtipuuvaneri valmistetaan yleensä ureaformaldehydihartsista.
Joissakin sovelluksissa vaaditaan vanerilevyjä, joissa on ohut kerros muovia, metallia tai hartsikyllästettyä paperia tai kangasta, joka on kiinnitetty joko etu- tai takapuolelle (tai molempiin), jotta ulkopinta kestäisi paremmin kosteutta ja hankausta tai jotta sen maalinpitävyys paranee. Tällaista vaneria kutsutaan päällekkäisvaneriksi, ja sitä käytetään yleisesti rakennus-, kuljetus- ja maatalousteollisuudessa.
Muut vanerilevyt voidaan päällystää nestemäisellä petsillä, jotta pinnat saavat viimeistellyn ulkonäön, tai niitä voidaan käsitellä erilaisilla kemikaaleilla vanerin liekinkestävyyden tai hajoamiskestävyyden parantamiseksi.
Vaneria on kaksi laajaa luokkaa, joilla molemmilla on oma luokitusjärjestelmänsä.
Yksi luokka tunnetaan nimellä rakennus- ja teollisuusvaneri. Tähän luokkaan kuuluvia vanereita käytetään ensisijaisesti niiden lujuuden perusteella, ja ne luokitellaan niiden altistumiskyvyn sekä etu- ja takapuolella käytetyn viilun laadun perusteella. Alastumiskyky voi olla sisä- tai ulkokäyttöön liiman tyypistä riippuen. Viilulaadut voivat olla N, A, B, C tai D. N-laadulla on hyvin vähän pintavirheitä, kun taas D-laadulla voi olla lukuisia oksia ja halkeamia. Esimerkiksi talon aluslattiana käytetty vaneri on luokiteltu "Sisäkäyttöön CD". Tämä tarkoittaa, että sillä on C-pinta ja D-kääntöpuoli, ja liima soveltuu käytettäväksi suojatuissa tiloissa. Kaikkien rakennus- ja teollisuusvanerien sisäviilut on valmistettu C- tai D-luokan viilusta luokituksesta riippumatta.
Toinen vaneriluokka tunnetaan lehtipuu- ja koristevanerina. Tämän luokan vanereita käytetään ensisijaisesti niiden ulkonäön perusteella, ja ne luokitellaan kosteudenkestävyyden mukaan laskevassa järjestyksessä teknisiin (ulkokäyttöön), tyyppiin I (ulkokäyttöön), tyyppiin II (sisäkäyttöön) ja tyyppiin III (sisäkäyttöön). Niiden pintaviilut ovat käytännössä virheettömiä.
Koot
Vanerilevyjen paksuus vaihtelee 1,6 mm:stä 76 mm:iin. Yleisimmät paksuudet ovat 6,4 mm:stä 19,0 mm:iin. Vaikka vanerilevyn ydin, poikkileikkaukset sekä etu- ja takapinta voidaan valmistaa eri paksuisista viiluista, niiden paksuuden on oltava tasapainossa keskiosan ympärillä. Esimerkiksi etu- ja takapinnan on oltava yhtä paksut. Samoin ylä- ja alaosan poikkileikkauksien on oltava yhtä suuret.
Yleisin rakennusalalla käytettyjen vanerilevyjen koko on 1,2 m leveä ja 2,4 m pitkä. Muita yleisiä leveyksiä ovat 0,9 m ja 1,5 m. Pituudet vaihtelevat 2,4 metristä 3,6 metriin 0,3 metrin välein. Erikoissovellukset, kuten veneenrakennus, saattavat vaatia suurempia levyjä.
Vanerin valmistukseen käytettävät puut ovat yleensä läpimitaltaan pienempiä kuin sahatavaran valmistukseen käytettävät puut. Useimmissa tapauksissa ne on istutettu ja kasvatettu vaneriyhtiön omistamilla alueilla. Näitä alueita hoidetaan huolellisesti puiden kasvun maksimoimiseksi ja hyönteisten tai tulipalojen aiheuttamien vahinkojen minimoimiseksi.
Tässä on tyypillinen toimintajärjestys puiden jalostamiseksi standardikokoisiksi 4 jalkaa x 8 jalkaa (1,2 m x 2,4 m) vanerilevyiksi:
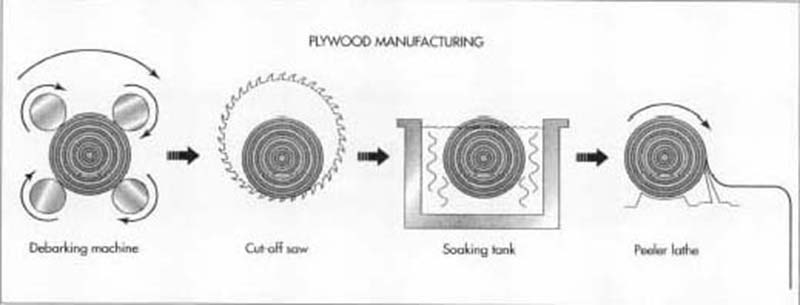
Tukit kuoritaan ensin ja sahataan sitten sormipaloiksi. Jotta palat voidaan leikata viilusuikaleiksi, ne ensin liotetaan ja sitten kuoritaan suikaleiksi.
1 Alueella valitut puut merkitään kaadettaviksi. Kaato voidaan tehdä bensiinikäyttöisillä moottorisahoilla tai pyörillä varustettujen ajoneuvojen, joita kutsutaan kaatajiksi, etuosaan asennetuilla suurilla hydraulisilla leikkureilla. Kaatuneiden puiden oksat poistetaan moottorisahoilla.
2 Leikatut puunrungot eli tukit raahataan lastausalueelle pyörillä varustetuilla ajoneuvoilla, joita kutsutaan juontotraktoreiksi. Tukit katkaistaan määrämittaan ja lastataan kuorma-autoihin kuljetettavaksi vaneritehtaalle, jossa ne pinotaan pitkiksi pinoiksi, joita kutsutaan tukkikansiksi.
3 Kun tukkeja tarvitaan, ne noudetaan tukkitasolta kumipyöräkuormaajilla ja asetetaan ketjukuljettimelle, joka kuljettaa ne kuorimakoneelle. Kone poistaa kuoren joko terävähampaisilla hiomalaikoilla tai korkeapaineisella vesisuihkulla, samalla kun tukkia pyöritetään hitaasti pituusakselinsa ympäri.
4 Kuoritut tukit kuljetetaan ketjukuljettimella sahalle, jossa valtava pyörösaha leikkaa ne noin 2,5–2,6 metrin pituisiksi paloiksi, jotka soveltuvat standardinmukaisten 2,4 metrin pituisten arkkien valmistukseen. Näitä tukkipaloja kutsutaan kuorimalohkoiksi.
5 Ennen viilun leikkaamista kuorimapalikat on lämmitettävä ja liotettava puun pehmentämiseksi. Palikat voidaan höyryttää tai upottaa kuumaan veteen. Tämä prosessi kestää 12–40 tuntia puulajista, palan halkaisijasta ja muista tekijöistä riippuen.
6 Lämmitetyt kuorimalohkot kuljetetaan sitten kuorimasorviin, jossa ne kohdistetaan automaattisesti ja syötetään sorviin yksi kerrallaan. Kun sorvi pyörittää lohkoa nopeasti pituusakselinsa ympäri, täyspitkä veitsen terä kuorii jatkuvan viilulevyn pyörivän lohkon pinnalta nopeudella 300–800 jalkaa/min (90–240 m/min). Kun lohkon halkaisija pienenee noin 3–4 tuumaan (230–305 mm), jäljelle jäävä puupala, joka tunnetaan nimellä kuorimaytime, työnnetään ulos sorvista ja uusi kuorimalohko syötetään tilalle.
7 Sorvista tuleva pitkä viilulevy voidaan käsitellä välittömästi tai se voidaan varastoida pitkille, monitasoisille alustoille tai kelata rullille. Joka tapauksessa seuraava prosessi sisältää viilun leikkaamisen käyttökelpoisiin leveyksiin, yleensä noin 1,4 m (4 ft-6 in), standardin 1,2 m (4 ft) leveiden vanerilevyjen valmistamiseksi. Samaan aikaan optiset skannerit etsivät osia, joissa on hyväksymättömiä virheitä, ja ne leikataan pois, jolloin jäljelle jää standardia leveyttä pienempiä viilupaloja.
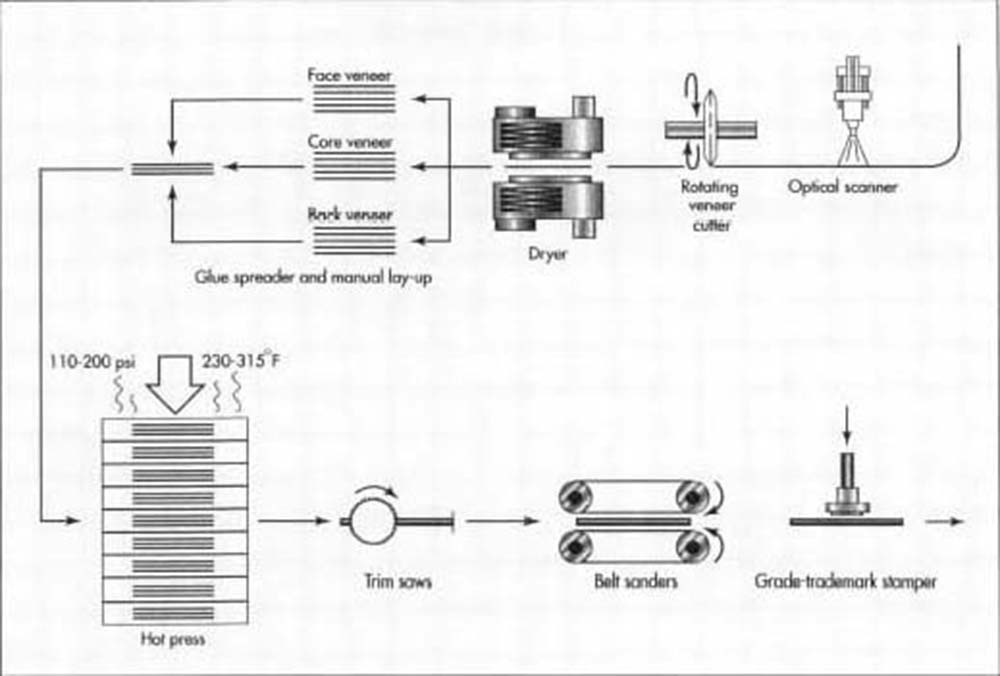
Märät viilukaistaleet kelataan rullalle, ja optinen skanneri havaitsee puussa mahdolliset hyväksymättömät virheet. Kuivumisen jälkeen viilu lajitellaan ja pinotaan. Valitut viiluosat liimataan yhteen. Kuumapuristimella viilu tiivistetään yhdeksi kiinteäksi vanerikappaleeksi, joka leikataan ja hiotaan ennen kuin se leimataan sopivalla laadulla.
8 Viilupalat lajitellaan ja pinotaan sitten laadun mukaan. Tämä voidaan tehdä manuaalisesti tai automaattisesti optisten skannerien avulla.
9 Lajitellut osat syötetään kuivaimeen, jossa niiden kosteuspitoisuus alenee ja ne kutistuvat ennen liimausta. Useimmat vaneritehtaat käyttävät mekaanista kuivainta, jossa kappaleet liikkuvat jatkuvasti lämmitetyn kammion läpi. Joissakin kuivaimissa kappaleiden pintaan puhalletaan suurnopeuksisia, lämmitettyjä ilmasuihkuja kuivumisprosessin nopeuttamiseksi.
10 Kun viilupalat tulevat kuivausrummusta, ne pinotaan laadun mukaan. Leveyden alapuolella oleviin paloihin on teipillä tai liimalla liitetty lisäviilua, jotta palat soveltuvat käytettäväksi sisäkerroksissa, joissa ulkonäkö ja lujuus ovat vähemmän tärkeitä.
11 Ne viilun osat, jotka asennetaan poikittain – ydin kolmikerroksisissa levyissä tai poikkinauhat viisikerroksisissa levyissä – leikataan noin 1,3 metrin (4 jalkaa-3 tuumaa) pituisiksi paloiksi.
12 Kun asianmukaiset viilupalat on koottu tiettyä vanerierää varten, alkaa kappaleiden kokoaminen ja liimaaminen yhteen. Tämä voidaan tehdä manuaalisesti tai puoliautomaattisesti koneilla. Yksinkertaisimmassa kolmikerroksisen levyjen tapauksessa taustaviilu asetetaan tasaiselle alustalle ja ajetaan liimalevittimellä, joka levittää liimaa yläpinnalle. Ydinviilun lyhyet palat asetetaan sitten poikittain liimatun taustan päälle, ja koko levy ajetaan liimalevittimellä toisen kerran. Lopuksi pintaviilu asetetaan liimatun ytimen päälle, ja levy pinotaan muiden puristimeen menevien levyjen kanssa.
13 Liimatut levyt ladataan moniaukkoiseen kuumapuristimeen. Puristimet pystyvät käsittelemään 20–40 levyä kerrallaan, ja jokainen levy ladataan omaan rakoonsa. Kun kaikki levyt on ladattu, puristin puristaa ne yhteen noin 7,6–13,8 baarin paineella ja samanaikaisesti lämmittää ne noin 109,9–157,2 °C:n lämpötilaan. Paine varmistaa hyvän kosketuksen viilukerrosten välille, ja lämpö saa liiman kovettumaan kunnolla maksimaalisen lujuuden saavuttamiseksi. 2–7 minuutin kuluttua puristin avataan ja levyt puretaan.
14 Karkeat levyt kulkevat sitten sahasarjan läpi, joka leikkaa ne lopulliseen leveyteensä ja pituuteensa. Korkealaatuisemmat levyt kulkevat 1,2 metriä leveiden hihnahiomakoneiden läpi, joilla hiotaan sekä pinta että tausta. Keskilaatuiset levyt pistehiotaan manuaalisesti karheiden alueiden puhdistamiseksi. Jotkut levyt ajetaan pyörösahanterien läpi, jotka leikkaavat pintaan matalia uria, mikä antaa vanerille teksturoidun ulkonäön. Lopputarkastuksen jälkeen mahdolliset jäljellä olevat viat korjataan.
15 Valmiisiin arkkeihin leimataan laatumerkki, joka antaa ostajalle tietoa rasitusluokasta, laadusta, tehtaan numerosta ja muista tekijöistä. Saman laatumerkinnän omaavat arkit sidotaan yhteen pinoiksi ja siirretään varastoon odottamaan lähetystä.
Aivan kuten sahatavaran kanssa, ei ole olemassa täydellistä vaneria. Kaikissa vaneripaloissa on tietty määrä vikoja. Näiden vikojen lukumäärä ja sijainti määräävät vanerin laadun. Rakennus- ja teollisuusvanerien standardit on määritelty tuotestandardissa PS1, jonka ovat laatineet Yhdysvaltain kansallinen standardointivirasto (National Bureau of Standards) ja American Plywood Association. Kovapuu- ja koristevanerien standardit on määritelty American National Standards Instituten ja lehtipuuvanerivalmistajien yhdistyksen (Leaf Plywood Manufacturers' Association) laatimassa ANSIIHPMA HP:ssä. Nämä standardit eivät ainoastaan määritä vanerin luokitusjärjestelmiä, vaan myös määrittelevät rakenne-, suorituskyky- ja käyttökriteerit.
Vaikka vanerin valmistuksessa puut hyödynnetään melko tehokkaasti – ne käytännössä puretaan osiin ja kootaan takaisin vahvemmaksi ja käyttökelpoisemmaksi kokonaisuudeksi – valmistusprosessissa syntyy silti huomattavaa jätettä. Useimmissa tapauksissa vain noin 50–75 % puun käyttökelpoisesta puumäärästä muuttuu vaneriksi. Tämän luvun parantamiseksi kehitetään useita uusia tuotteita.
Yksi uusi tuote on nimeltään oriented strandboard (suuntaistettu lastulevy), joka valmistetaan silppuamalla koko tukki säikeiksi sen sijaan, että viilu kuoritaisiin tukista ja ydin poistettaisiin. Säikeet sekoitetaan liiman kanssa ja puristetaan kerroksiksi, joissa syyt kulkevat yhteen suuntaan. Nämä puristetut kerrokset asetetaan sitten toisiinsa nähden suorassa kulmassa, kuten vanerissa, ja liimataan yhteen. Oriented strandboard on yhtä vahvaa kuin vaneri ja maksaa hieman vähemmän.
Julkaisun aika: 10. elokuuta 2021